Design of a washing machine with double rotating drum
We have designed an innovative front-loading washing machine that washes better, in less time and using less detergent than traditional ones.
- Sector: Home appliances
- Target: Improve the washing quality of a front-loading washing machine, while reducing cycle times and lowering detergent consumption.
- Solution: Washing machine with double rotating drum
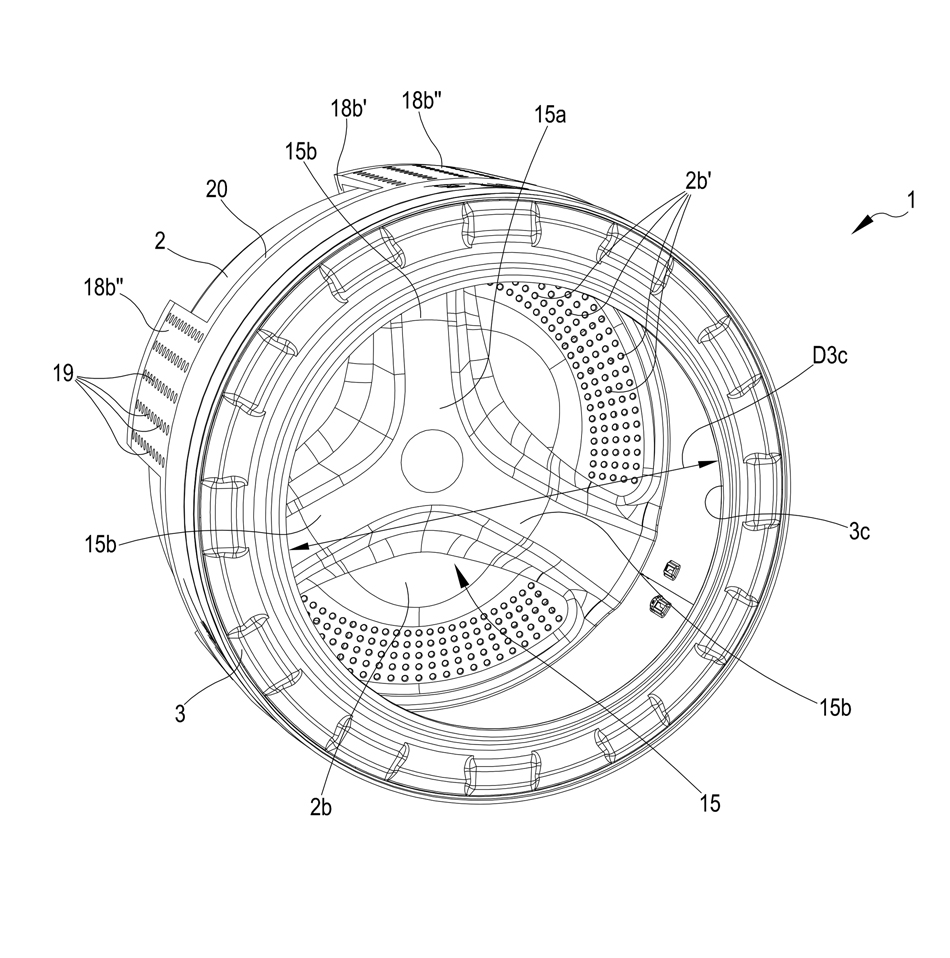
The background
The performance of one of Samsung’s design is not sufficient.
The Korean manufacturer Samsung has tried to revive this concept by creating a machine where the rear of the drum rotates in the opposite direction from the front.
Samsung's solution basically takes up the same concept of top loading machines, but loses effectiveness because the laundry inside the drum – especially when washing full loads – cannot always be moved by the counter-rotation of the rear drum section.
The idea
By using a drum where the two halves are rotated independently of each other, we can increase the effectiveness of the rubbing action on the laundry.
This improves the agitation even with small loads, and improves therefore the quality of the washing.
The challenge
A completely new product comes with many questions that need answering.
- Study a suitable anchoring system for the front half against the movement of the rear half.
- Structural verification of the assembly.
- Ensure that there is no friction in the facing between the two halves of the drum.
- Ensure that the washing items cannot remain trapped in the facing area between the two halves of the drum.
- Size the driving mechanisms of the two halves of the drum so as to provide the required dual rotation while, at the same time, keep the energy consumption at acceptable levels.
- Design the entire new assembly ensuring the same load capacity in the same overall cabinet dimensions of the washing machine.
The solution
Using calculations, simulations and laboratory tests on the prototype, we were able to validate the mechanical aspects of the structure.
The progress
The patent
In 2019, the innovation proposed by SPM has been the subject of a patent No. 102019000004031 for a front-loading washing machine with double rotating drum
Design of a control software
With the support of a specialist, we created an electronic control board and its appropriate control software to develop ad-hoc test washing cycles.
- Direction of rotation of the two drums.
- Duration of the rotation.
- Loading and discharge of water.
- Control of the heating element.
Performing washing tests
A certified body confirms that our solution is better than the traditional washing method.
Using our CAD system, we studied and prototyped a range of different paddle shapes inside the drum that could move the items during the wash while not generating tearing forces when the two halves of the drum turn in opposite directions.
Rinsing and spinning were carried out on a commercially-available machine, since we could not perform these operations on our prototype, while the entire washing cycle was tested on the new application.
The tests were carried out using a standard stain set as required by IEC regulations.
Once we had obtained the desired results, we contacted a certified body to obtain an official report that established how the cycle defined as “alternative”, that is, the washing cycle of our product, gives better results than a “normal” one having the same duration.
The process
- Discussion with motor supplier to select the most suitable type of motor for the application.
- Creation of control hardware and software.
- Laboratory activities aimed at assembling the motors and the new control electronics.
- 3D modelling of different shapes of paddles.
- Construction and confirmation testing of paddles.
- Washing cycle programming.
- Cycle testing and comparative tests against traditional washing cycles without standard stain set.
- Cycle testing and comparative tests against traditional washing cycles with standard stain set.
- Execution of tests at a certified laboratory.